CONFERENCE HEIDELBERG
One of the questions frequently asked by customers when it comes to applying the stamping technique is whether the cold foil or Hotfoil style is more suitable. There’s no conclusive reply to this question, as it will depend on the type of work and the result to be achieved, as well as other considerations that will be taken into account to determine the ideal process to be followed. Ángel Pérez, marketing and e-commerce director at Heidelberg Spain, and Ignacio Baquero, Product Manager Sheetfed Business Driver HSP at the same company, offered some keys to differentiating between the two techniques and how to choose the more suitable one.
Hotfoil and Coldfoil are two options that reflect what kind of printing we want to do during graphic work. Moreover, we generally discuss packaging, which is what they’re most used for, but we can also refer to commercial printing in some cases.
One of the most significant differences? Hotfoil printing works very well for precise applications and defined patterns in small areas. Coldfoil printing, on the other hand, is the preferred technique for large areas, such as moderate or full coverage of folding boxes.
Customisation-related considerations must also be taken into account, as Hotfoil printing permits stamping on a sheet or embossment, while Coldfoil printing gives us control over the colour options by means of inline work.
The objectives determine the choice
Coldfoil is an inline process and a technology that’s been on the rise in recent years. Not surprisingly, more than eight facilities of this kind have been built in Spain. This technique uses a thin metallic layer that’s placed on top of the paper and the ink is printed onto the sheet. The metallic layer shows through the ink to achieve shiny and reflective effects. Coldfoil printing can offer a photographic image with gradients and shading while the Hotfoil kind is limited to a single flat colour.
During the cold lamination process, a UV curable adhesive is printed onto the substrate in the shape of the design to be laminated. The sheet is then pressed onto the material and removed in the areas where the adhesive isn’t printed. The product is completed following a quick run under ultraviolet light.
Coldfoil is available in a wide range of patterns and colours and no tools are required for the process. It can also be easily overprinted and used with heat-sensitive materials.
Hotfoil, on the other hand, is an offline process involving the hot stamping of an opaque sheet onto a support. The major difference lies in the way the sheet is deposited on the surface; in this case the metal sheet is deposited on the chosen support by means of a strong heat process. For example, when we print directly onto the cardboard, the latter can no longer be post-printed, so this involves a post-printing process, unlike Coldfoil, which is a process that forms part of the printing. This sheet works very well for text or minimal shapes and designs and it’s the preferred technique for those seeking a clean and highly detailed finish. Hotfoil lamination can be combined with stamping to produce a tactile effect, something which can’t be achieved with cold aluminium paper.
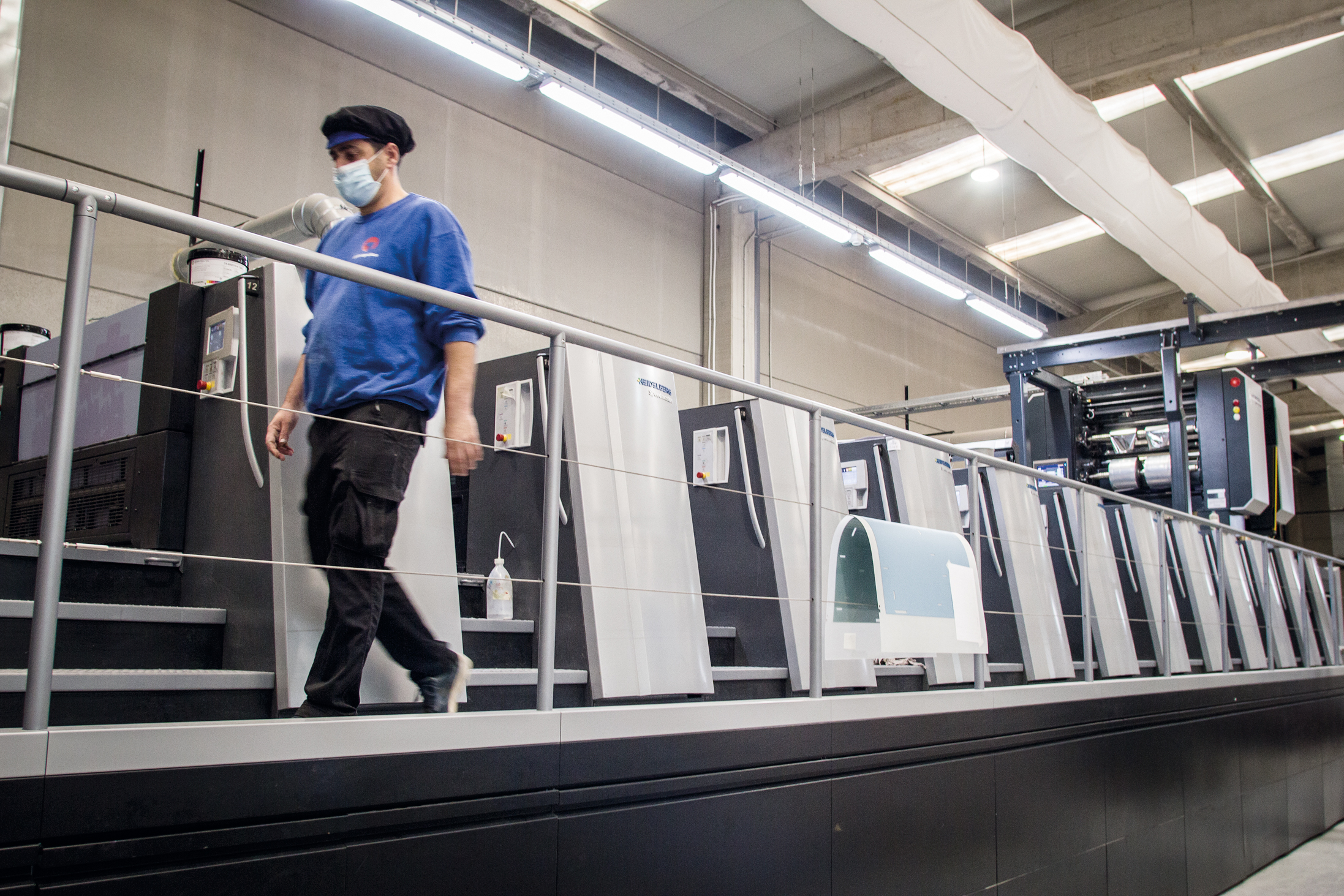
The hot stamping sheet has a luxuriously rich and embossed appearance. Very fine lines and text in numerous different colours and patterns can be incorporated into the packaging designs. In this respect, the embossment that can be achieved with Hotfoil are a little more accurate than with Coldfoil. On the other hand, one of the drawbacks of Hotfoil is the speed we usually work at (6,000 copies/hour), below that of the die-cutting technique, whereas Coldfoil has the speed of a printing press (around 18,000 copies/hour). In this regard, the differences in terms of productivity levels and the final output are also important. Long runs, for which Coldfoil is more useful, provide excellent results on covers.
If we need to fulfil a very large printing task, setting up a Hotfoil machine takes up a lot of time. In contrast, preparing a Coldfoil model simply entails setting up a plate. When we talk about Coldfoil, we refer to a printing plate, whereas Hotfoil involves a die-cutting process. Therefore, the cost of Hotfoil printing is higher at the beginning, regardless of the result we want to achieve.
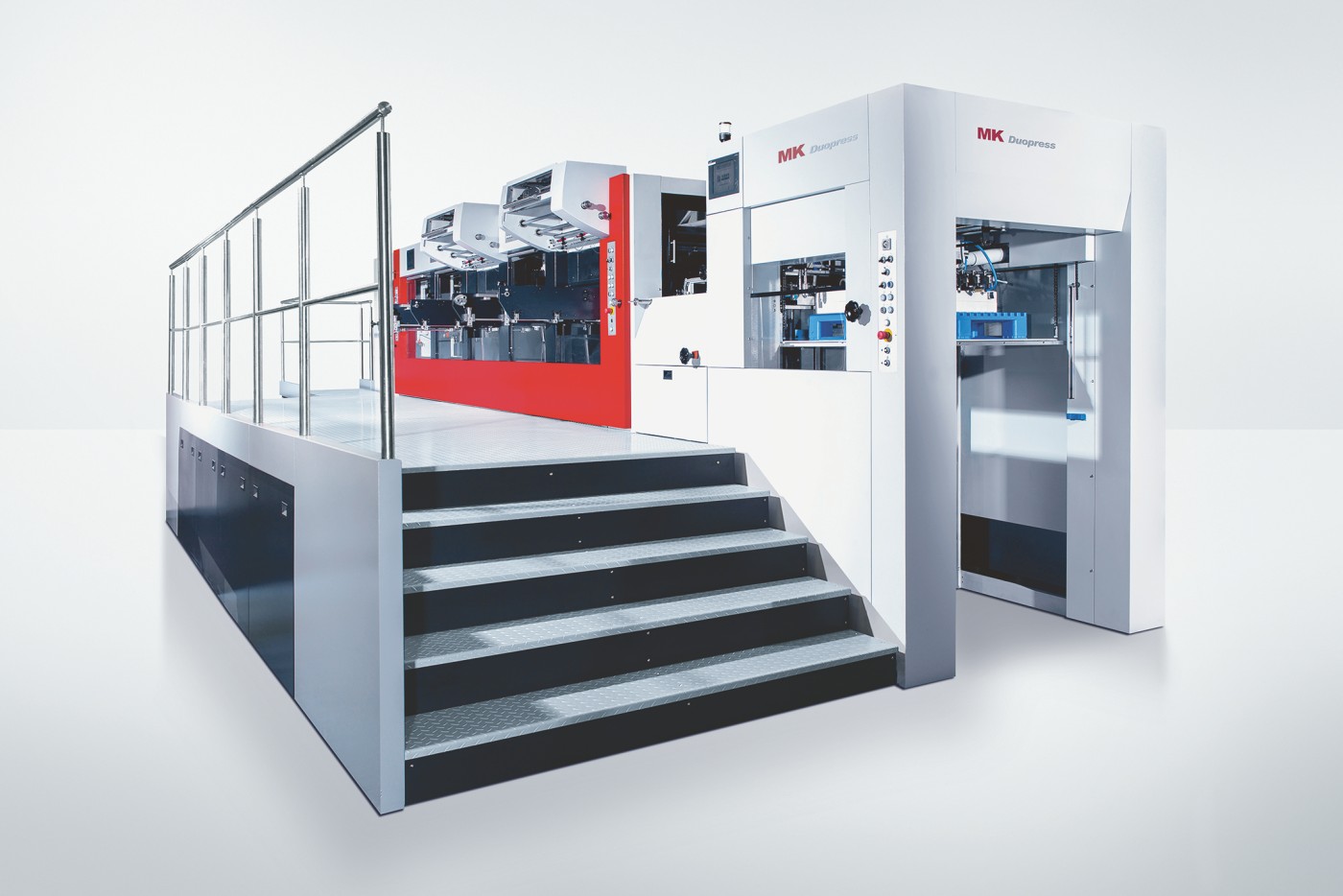
There is no generic ideal solution for all projects, as each product has its own raison d’être. Regardless of the machine we use and the technology, whether it be hot or cold, what we must bear in mind is that cold printing generates much less waste than the hot kind. The reason is that the sheet is recycled when cold, whereas when it’s hot we lose a little more during the process.
In short, the two technologies are not mutually exclusive, as both are focused on different types of products and print runs, and they may even be complementary in some cases.
Comparison:
COLDFOIL | HOTFOIL |
It’s a printing process | It’s a post-printing process |
The equipment is a module on one of the printing units. | It’s a die-cutting machine |
It needs a plate | Die |
Less detail | Finer details |
Cheaper pigment | Resistant sheet |
Less waste | More waste |
UV curable adhesive | Pressed hot |
The support laminated as waste can be re-pulped. Easily recyclable. | It’s expensive and difficult to delaminate, making it a non-recyclable support. |
It consumes less energy and it’s faster | It consumes more energy and it’s slower |
*Source: Heidelberg